In this post we will show you how you can calibrate a Torque Wrench.
Here we calibrate a SMA Torque Wrench, but the method shown here are applicable to common Torque Wrenches.
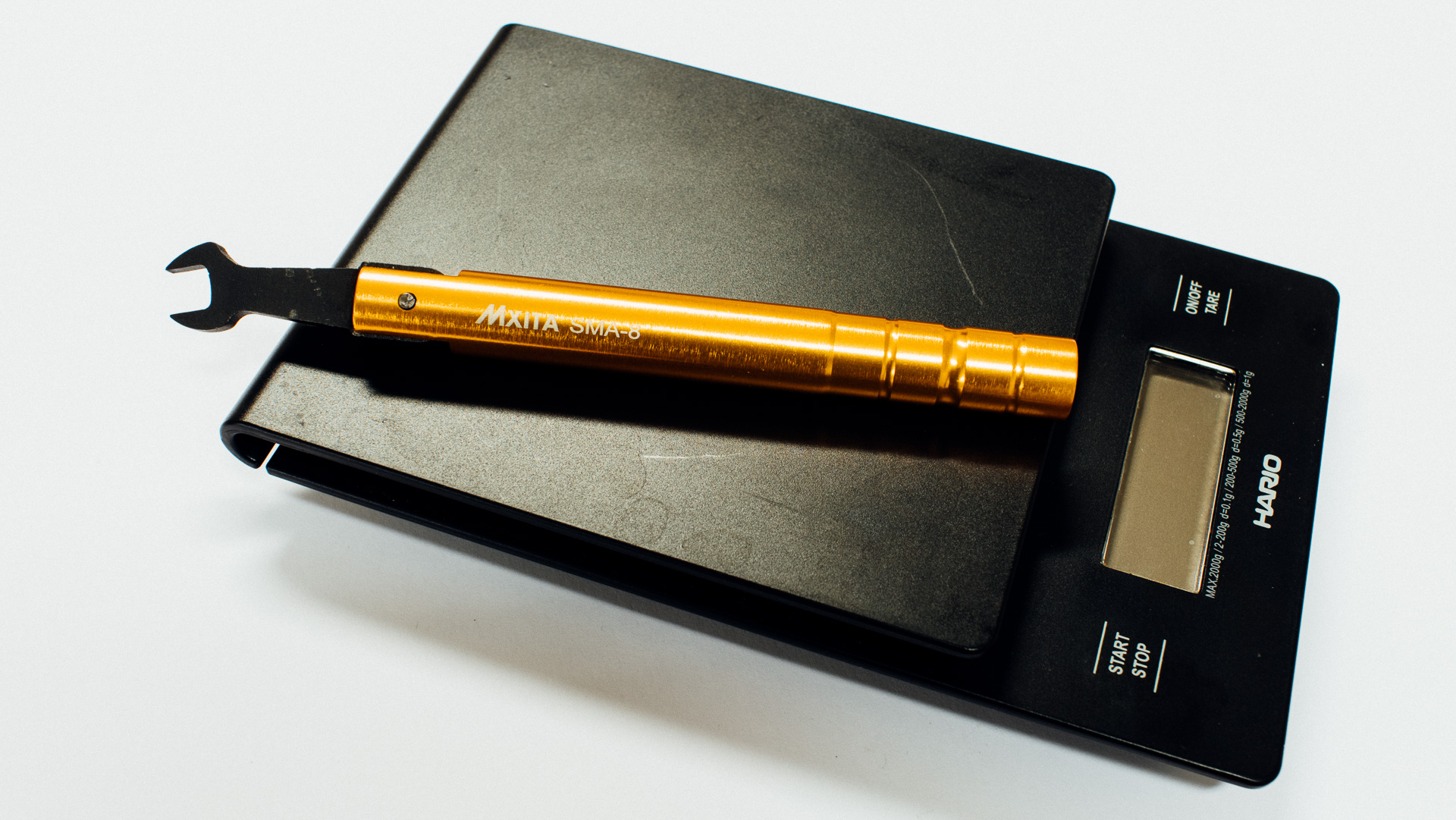
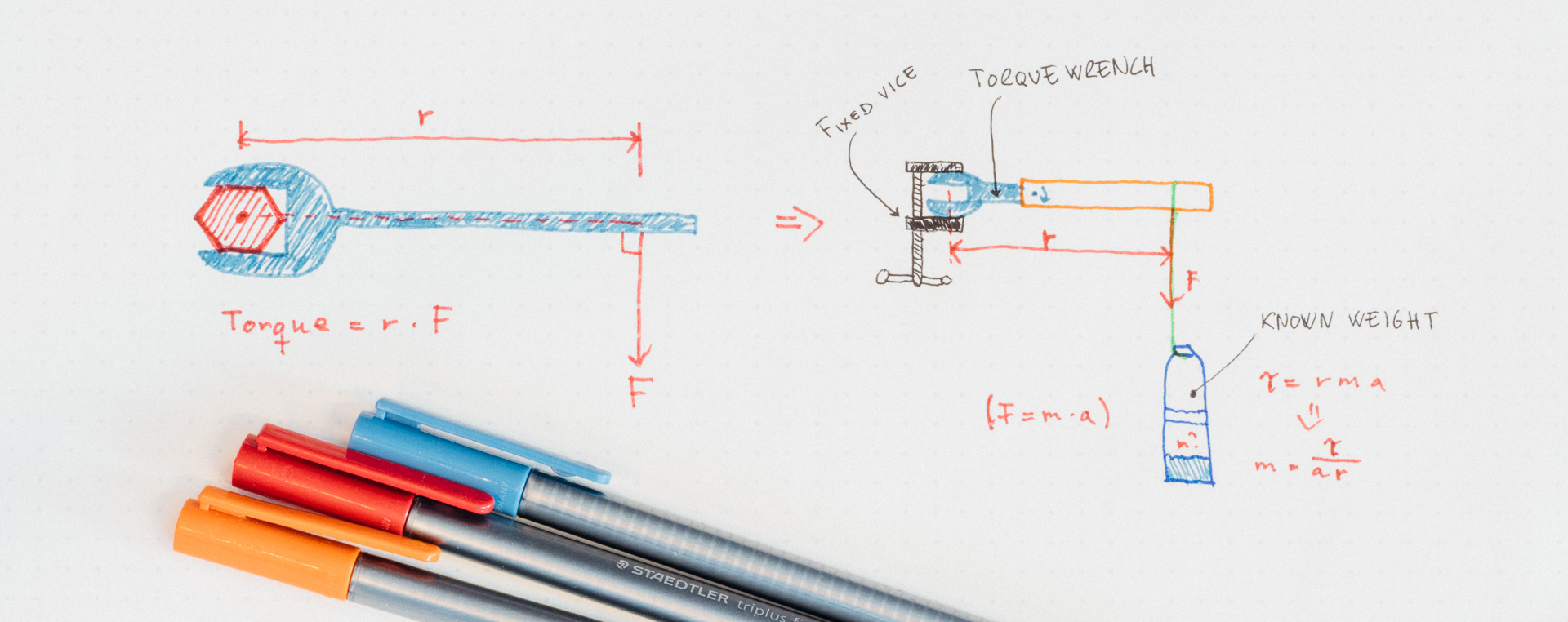
1. Gathering necessary information and tools
The wrench we are calibrating here is a fixed Torque Wrench, but a variable Torque Wrench can be calibrated almost in the same manner, but check the specific Wrench user manual.
We decided to fix the torque value for this Wrench at 0,4 Nm. That was among other things based on what the Wrench was going to be used to.
You can read more about SMA connectors here.
2. Measure the Calibration distance (on the Wrench)
Find an appropriate location on the handle. E.g. a groove as shown here.
After you have decided what point to hang your calibration load from, you have to measure the distance from that point to the CENTER of the Wrench drive.
This distance finding can be achieved in several ways. The easiest (and maybe best) are if you have access to digital mechanical drawings of the wrench and can extract the necessary information from there.
But if nothing better is possible, you can do as here: Manual measuring.
We found that the distance on the Wrench being calibrated here was ~136 mm.
3. Prepare the Calibration load
We know Torque and Length. The Gravity is approx 9,8 m/s2, but location dependent gravity can be calculated, and a simple online tool to help you with that can be found here.
If we insert our data into the equation above, we get out that we should apply a load on ~300 g on the Torque Wrench to make it “let go“.
With that number in mind, we found an old bottle, added some rope for Torque Wrench attachment, and filled it with enough water so everything weighed total ~300 grams.
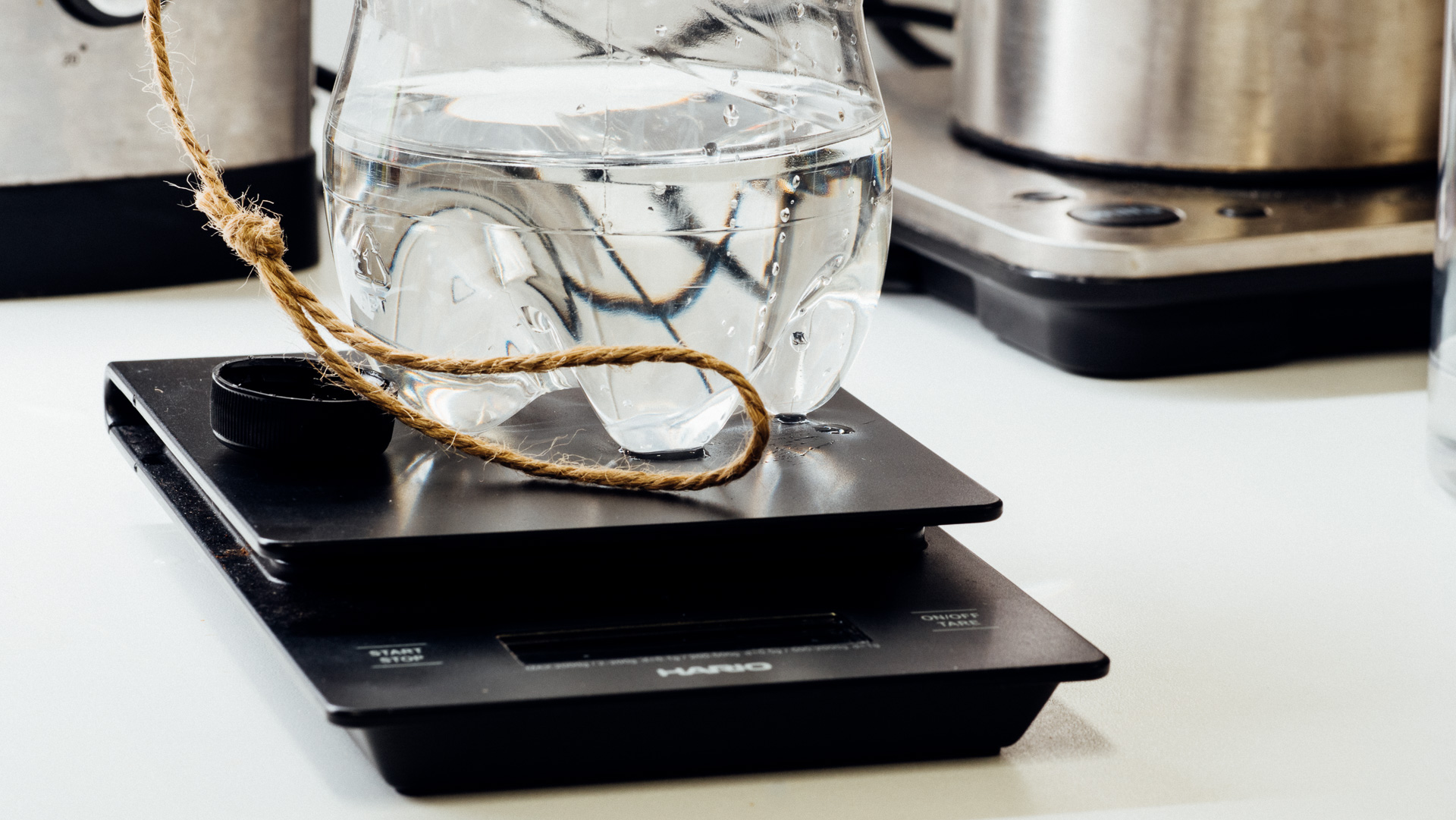
4. Calibrate the Wrench
After we had made the Calibration Load, we securely attached the Wrench head to a vice.
We located the set-screw and tightened it to make sure we started in a known Calibration state.
The set-screw adjusts the torque settings
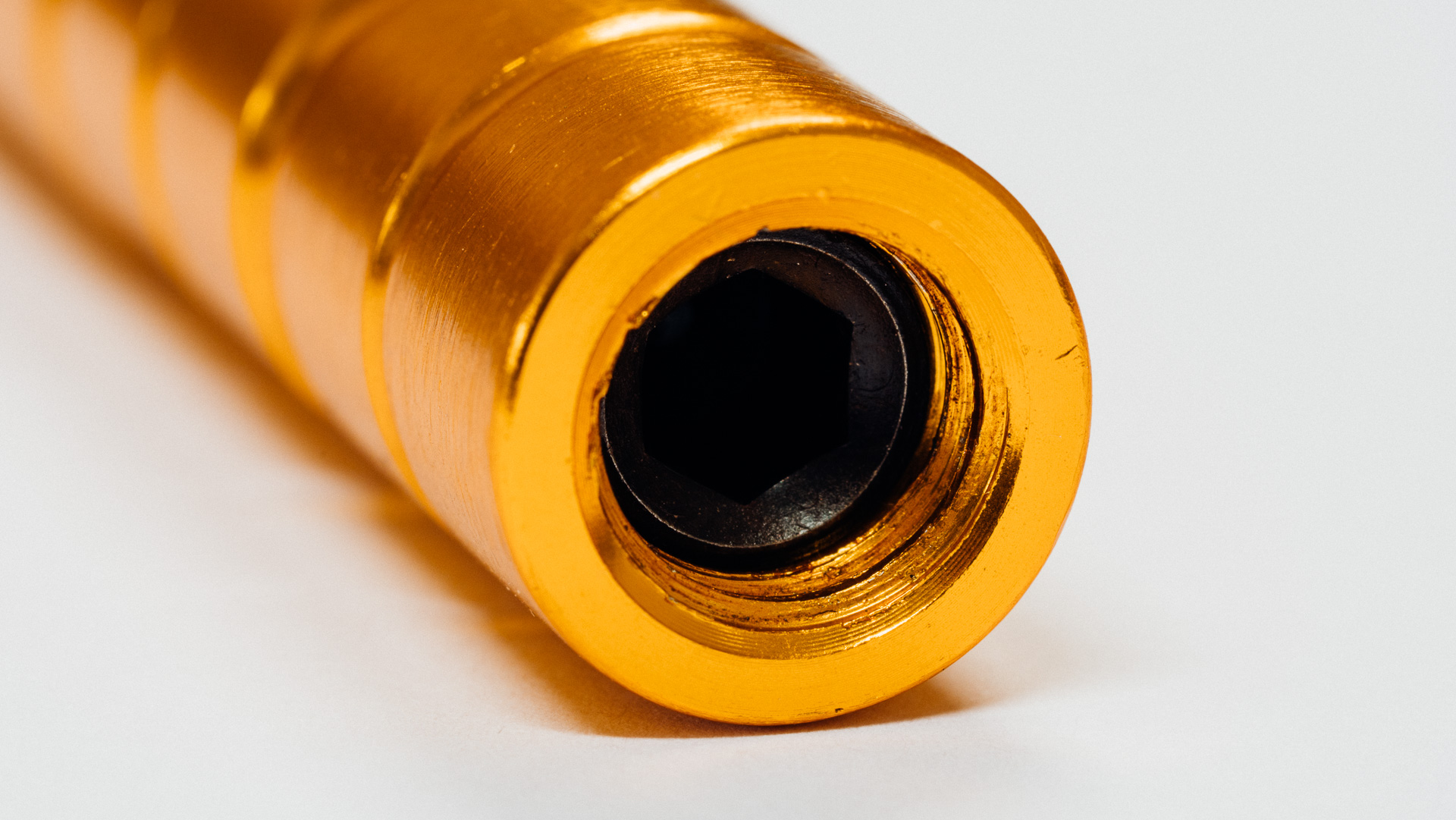
After we had increased the Torque Wrench set point, we hung the calibration load on the appropriate groove.
After that was done, we adjusted the set screw back-and-forth until we had found a spot where the Torque Wrench did “let go” exactly in the right moment.
Final Words
Torque Wrench type and usage plays an important role when it comes to “how often should it be Calibrated?“. Remember that and:
Happy calibrating!
The Torque Wrench calibrated here will probably be used in an upcoming blog post!